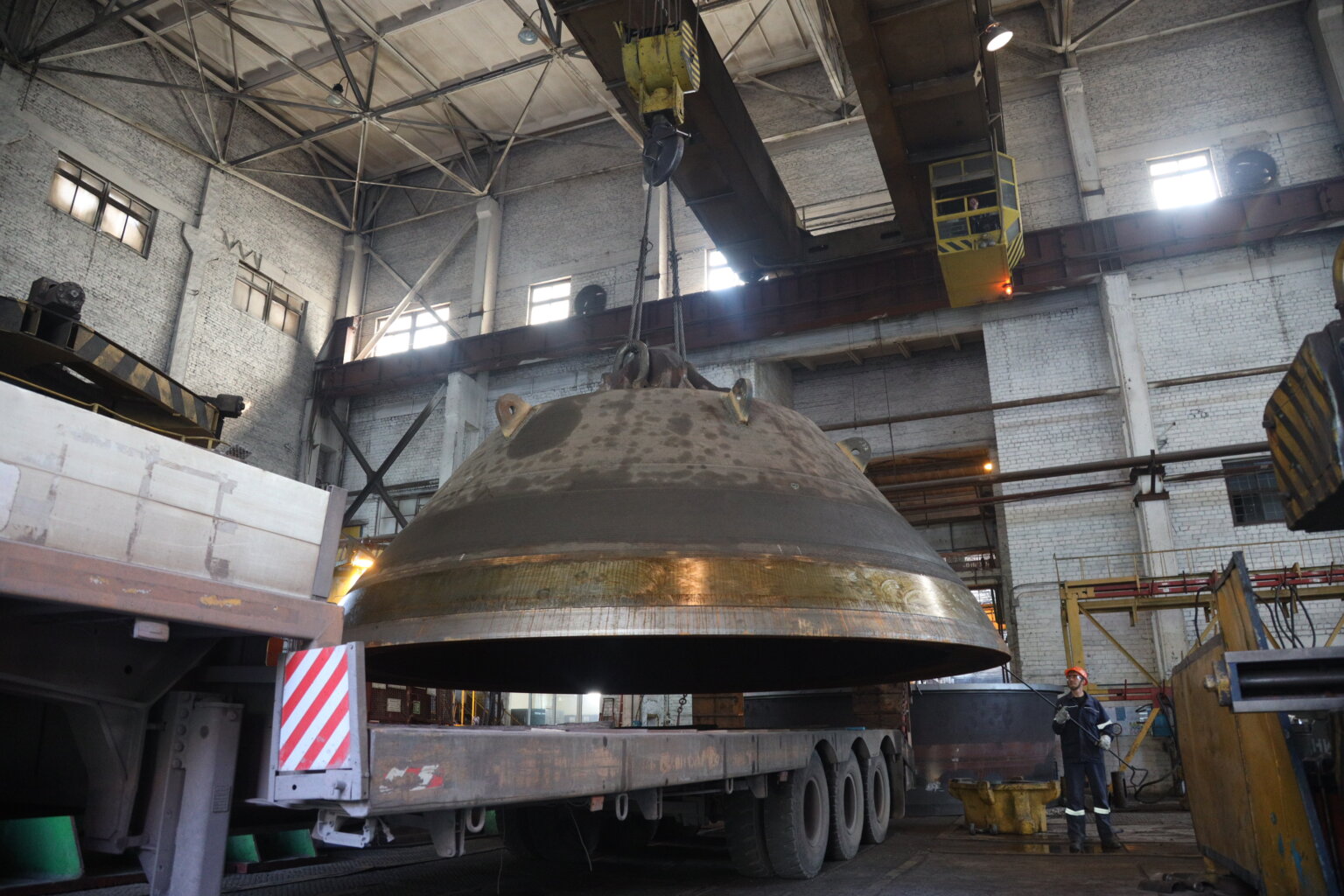
«Guesswork»
Our plant's workers have manufactured the main equipment for blast furnace № 8.
Recently, the ArcelorMittal Kryvyi Rih enterprise completed a major overhaul of blast furnace №8. The main equipment for the furnace - the charging device, the traction device, the coke and agglomerate screens, the skip for transporting the charge - were manufactured by СMP workers. Currently, the equipment is installed on the blast furnace and performs its functions.
The charging device is the most massive and, perhaps, the most difficult to manufacture from this list of equipment. It is used to load the charge into the blast furnace shaft. The device consists of a bowl weighing 22 tons and a cone inserted into it weighing 27 tons. The diameter of the bowl base is almost 7 meters. Our CMP manufactured the bowl elements, as they say, from scratch. The complexity of production was also in the fact that the castings had to be processed with jewelry precision and the necessary resistance of the products to high temperatures, aggressive environments and mechanical damage had to be achieved.
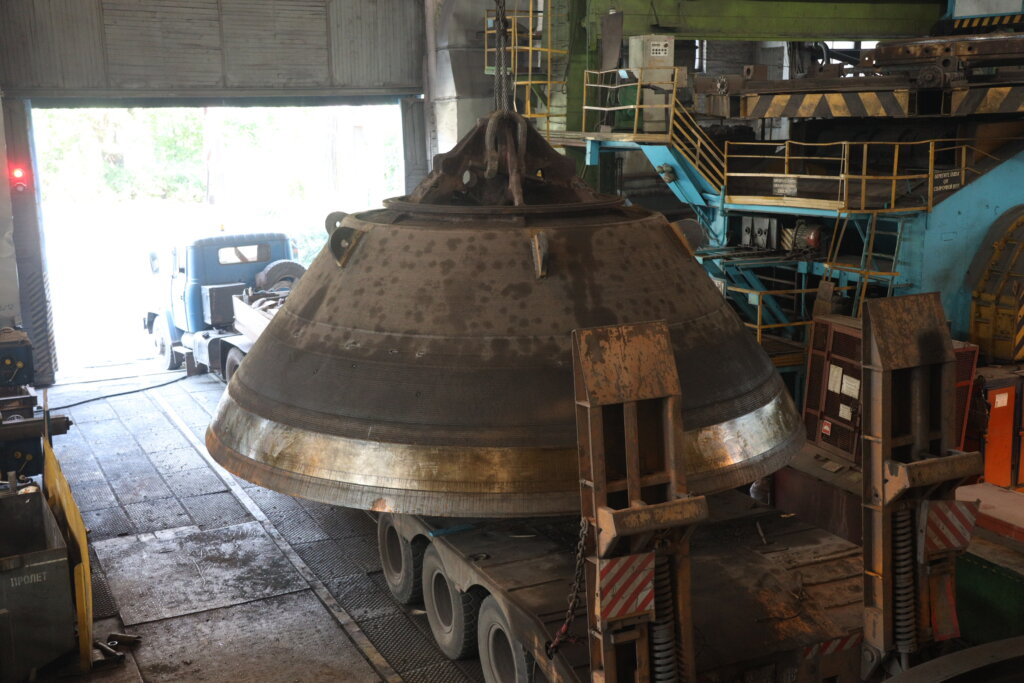
All the castings, that is, the blanks for the bowl and cone, were made by specialists from the steel foundry. The top of the bowl, its bottom, and the same with the cone were cast separately. “First, we made models and large molds for the castings. Modeler Evgeny Kovrik, molder Evgeny Yurchenko and others worked on this. Then steelmakers Anton Temnikov, Vladimir Skaliga, Yuri Gaber and their colleagues welded steel with the necessary properties in furnaces, and caster Vitaly Savko and his colleagues poured this steel into the mold. Then the knockout workers, including Evgeny Nepsha, released the blanks from the molds, and workers from the cutting section Bogdan Borsch, Vladimir Degtyarev and others cut off and chopped off all the excess metal elements formed during the pouring of steel. After this, the castings were heat treated in a huge thermal furnace. According to Evgeny Konovalov, the SFS has a heat-treating furnace the size of a building. Its working space is almost seven meters wide, more than eight meters long, and five and a half meters high.
The machining of the huge castings was performed on a unique KU-101 vertical turning lathe. The excess metal layer was removed to bring the geometric parameters in line with the drawings. The machining on the machine took place in several stages, between which the lower and upper elements of the bowl and cone were welded together, and the surfaces of their joints were welded using high-quality welding wire. This gave the surfaces strength, but also complicated the machining, because hard materials are more difficult to process. But the MRS-1 team did a good job, grinding the joint surfaces to ensure a tight fit between the bowl and cone.
The head of MRS-1 Evgeniy Grechany, admitted that it was not easy, because three of the four KU-101 machine operators were mobilized into the ranks of the Armed Forces of Ukraine, and operating such a machine requires high qualifications.
"Indeed, the workers had to be trained in an accelerated mode. One of them had previously worked as a blacksmith, says Evgeniy Grechany. - The team of Igor Shostak, Daniil Grishaev, Evgeniy Khlivny and Nikolay Chervotoka, who returned to the shop after demobilization, coped. To our greatest regret, Vladimir Slyusar, who had been in charge of KU-101 before mobilization, was killed in action. We will always remember him. I would also like to thank welders Sergey Popov and Valentin Karmanov, milling machine operators Vladimir Kovbaskin and Vyacheslav Kildyushov, who also distinguished themselves during the processing of the filling device elements." Sergey Shokotko, a production mechanic at the central maintenance and repair department, coordinated the interaction of departments during the overhaul of BF-8. "The work on manufacturing equipment for BF-8 took place in difficult conditions," Sergey noted.
There were tendencies toward early completion of the work. Life made adjustments, but CMP met the planned deadline. Together we are working to increase the service life of charging devices and other equipment manufactured by CMP shops, and we are succeeding. We hope that the recently manufactured equipment will show itself in the best possible way in the production of cast iron."